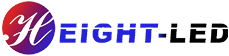
In the electronics production industry, UVLED curing technology has been increasingly used in large-scale industrial production.
Many manufacturers use environmentally friendly and efficient UVLED curing machines to replace less environmentally friendly UV mercury
lamps. UVLED curing machines can replace mercury lamps on the one hand because of their environmental protection characteristics, and
on the other hand because of their fast curing and high efficiency and energy-saving features, which are very suitable for assembly line
operations. UVLED curing has the following main application points in the electronics industry.
1.PCB circuit board UV electronic protective glue curing.
The circuit board is the core part of electronic equipment, and its production is divided into two steps. First, the required circuit
is etched on the copper film by using the circuit etching ink, and then the copper circuit is covered and protected with solder resist ink
to prevent damage during component welding. For circuit boards with extremely high precision requirements and complex use environments, a
layer of UV electronic protective glue can be wrapped as a whole after soldering all electronic components,which is waterproof,dustproof
and shockproof. Then go through the UVLED curing.
2.UVLED curing on the surface of the case.
Undoubtedly, this is the most common and widely used place, and it embodies most of the unique advantages of UVLED curing technology. The UV
varnish cured by UVLED curing technology can be completely completed in only a few seconds to about a second. Curing. The curing process does not
require high-temperature baking, does not cause problems such as deformation of the casing, saves energy and high efficiency, and reduces the
reject rate.
The cured product is free of volatile organic residues, non-toxic and harmless, and the workpiece after intense ultraviolet radiation is also
completely sterilized. The gloss of the coating film can be adjusted freely from the highest light to the full matte. With a variety of substrates
and primers, it can produce a wide range of surface effects. The entire coating is made into a whole through chemical reaction, which is extremely
wear-resistant and scratch-resistant.
3.LCD adhesive UV curing
The liquid crystal display can be roughly regarded as a thin glass sheet encapsulated with a layer of liquid crystal. The liquid crystal cannot be
heated and cannot be polluted. Only UV glue and UVLED curing machine can be cured instantly and no heating is required. Requirements, such as TFT-LCD
liquid crystal panel FPC paste packaging.
In addition, there are many places in the communication industry that use UVLED curing machines, such as optical communication industry source devices
(PLC splitter, wavelength division multiplexer WDM, array grating waveguide AWG, etc.) Connection or potting, fixing of small components, etc.), staining paint
for glass fiber in communication cables, resist in semiconductors, photoresist, etc.